Save Time and Money with Effective Packaging Machine Repair Services
Save Time and Money with Effective Packaging Machine Repair Services
Blog Article
Quick and Reliable Packaging Machine Repair Service Provider to Lessen Downtime
In the competitive landscape of manufacturing, the effectiveness of packaging procedures pivots on the integrity of machinery. Quick and dependable repair service solutions are important in alleviating downtime, which can lead to significant operational problems and economic losses.
Value of Timely Repair Works
Timely repair services of packaging devices are important for maintaining functional efficiency and decreasing downtime. In the busy setting of manufacturing and product packaging, even minor malfunctions can bring about substantial hold-ups and performance losses. Resolving concerns promptly makes certain that devices run at their optimum capacity, consequently guarding the circulation of procedures.
Additionally, normal and prompt maintenance can prevent the acceleration of minor problems into major failures, which frequently sustain greater fixing expenses and longer downtimes. A positive technique to equipment repair work not just maintains the stability of the devices but likewise enhances the general integrity of the assembly line.
In addition, prompt repairs add to the longevity of product packaging machinery. Devices that are serviced without delay are less most likely to experience from excessive damage, permitting organizations to maximize their financial investments. This is specifically essential in industries where high-speed product packaging is essential, as the demand for consistent efficiency is paramount.
Benefits of Reliable Provider
Reputable solution suppliers play a pivotal role in making certain the smooth operation of packaging devices. Their competence not just boosts the effectiveness of repair services but additionally adds dramatically to the long life of devices.
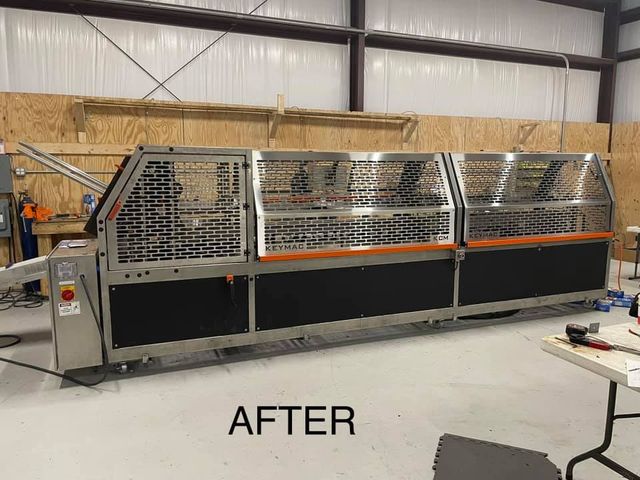
Additionally, a trustworthy solution provider supplies extensive support, consisting of training and support for personnel on device procedure and upkeep finest techniques. This not only equips employees but also cultivates a society of safety and effectiveness within the company. Overall, the advantages of engaging dependable provider expand beyond immediate repairs, positively impacting the entire functional operations of packaging processes.
Typical Packaging Machine Problems
In the world of packaging procedures, different problems can compromise the effectiveness and capability of machines. One common trouble is mechanical failing, usually originating from damage or inadequate upkeep. Elements such as electric motors, belts, and gears might fall short, leading to breakdowns that halt production. One more common concern is imbalance, which can cause jams and unequal product packaging, impacting item top quality and throughput.
Electric troubles can additionally interfere with packaging operations. Damaged electrical wiring or malfunctioning sensors might cause irregular device behavior, creating hold-ups and enhanced operational expenses. Additionally, software application glitches can prevent the equipment's shows, leading to operational inefficiencies.
Irregular item circulation is one more crucial problem. This can arise from variations in item size, form, or weight, which may impact the machine's capability to handle things precisely. Inadequate training of drivers can intensify these issues, as untrained workers may not acknowledge early indicators of breakdown or might abuse the equipment.
Dealing with these common product packaging equipment concerns without delay is essential to keeping performance and guaranteeing a smooth operation. Routine evaluations and positive maintenance can substantially minimize these concerns, cultivating a reliable packaging setting.
Tips for Minimizing Downtime
To lessen downtime in packaging operations, executing a proactive maintenance method is important. Regularly scheduled maintenance checks can recognize potential issues prior to they intensify, ensuring makers run efficiently. Developing a regimen that consists of lubrication, calibration, and assessment of crucial elements can dramatically lower the regularity of unforeseen failures.
Training team to run equipment correctly and acknowledge early caution signs of breakdown can additionally play a vital duty. Encouraging operators with the expertise to execute basic troubleshooting can stop minor concerns from causing major delays. Keeping a well-organized supply of crucial spare parts can quicken repair services, as waiting for components can lead to prolonged downtime.
In addition, documenting device efficiency and maintenance activities can assist determine patterns and recurring problems, permitting targeted interventions. Incorporating advanced surveillance innovations can supply real-time data, enabling anticipating upkeep and lessening the threat of sudden failings.
Last but not least, fostering open interaction in between operators and maintenance teams makes sure that any kind of irregularities are quickly reported and attended to. By taking these aggressive measures, companies can improve functional performance and considerably reduce downtime in packaging processes.
Selecting the Right Repair Work Solution
Selecting the appropriate repair solution for product packaging machines is a crucial choice that can significantly affect operational efficiency. A well-chosen provider makes certain that your equipment is fixed swiftly, successfully, and to the highest possible criteria. Begin by examining the service provider's experience with your specific kind of packaging equipment. A specialist acquainted with your equipment can detect issues more properly and implement solutions extra swiftly.
Following, take into consideration link the provider's credibility. Seeking responses from other organizations within your industry can give insights into integrity and high quality. Qualifications and partnerships with identified equipment makers can additionally indicate a dedication to quality.
Additionally, examine their feedback time and availability. A provider who can use punctual support lessens downtime and maintains manufacturing flow stable. It's likewise crucial to ask regarding service warranty and service assurances, which can reflect the confidence the company has in their job.
Final Thought
In verdict, the value of trustworthy and quick packaging machine repair solutions can not be overstated, as they play a vital duty in reducing downtime and making certain operational efficiency. By focusing on timely repair services and selecting reputable company, companies can effectively attend to common problems and preserve efficiency. Implementing positive upkeep practices and spending in team training further click reference improves the longevity of packaging equipment. Inevitably, a tactical strategy to repair services promotes an extra resilient production setting.
Timely repairs of Extra resources packaging devices are vital for keeping functional performance and minimizing downtime.Additionally, timely repairs contribute to the longevity of product packaging equipment. On the whole, the advantages of involving trusted solution carriers expand past instant repair services, favorably affecting the entire operational workflow of product packaging procedures.
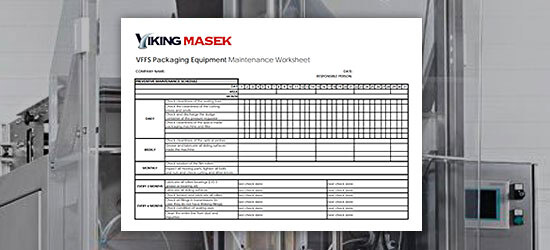
Report this page